Solutions for Efficient and Reliable Bagging Equipment Selection
In the fast-paced world of manufacturing and logistics, selecting the right bagging equipment is crucial for ensuring efficiency and reliability in your processes. Whether you are in the food, chemical, or agricultural sector, the performance of your bagging systems can significantly impact your productivity and bottom line. However, with a myriad of options available on the market, identifying a quality supplier can be a daunting task. This blog aims to guide you through the essential steps to finding top-notch bagging equipment providers, with a focus on understanding your specific needs, evaluating supplier capabilities, and leveraging industry insights. By the end of this article, you will be equipped with practical strategies to make informed decisions that enhance your operations and support long-term success.
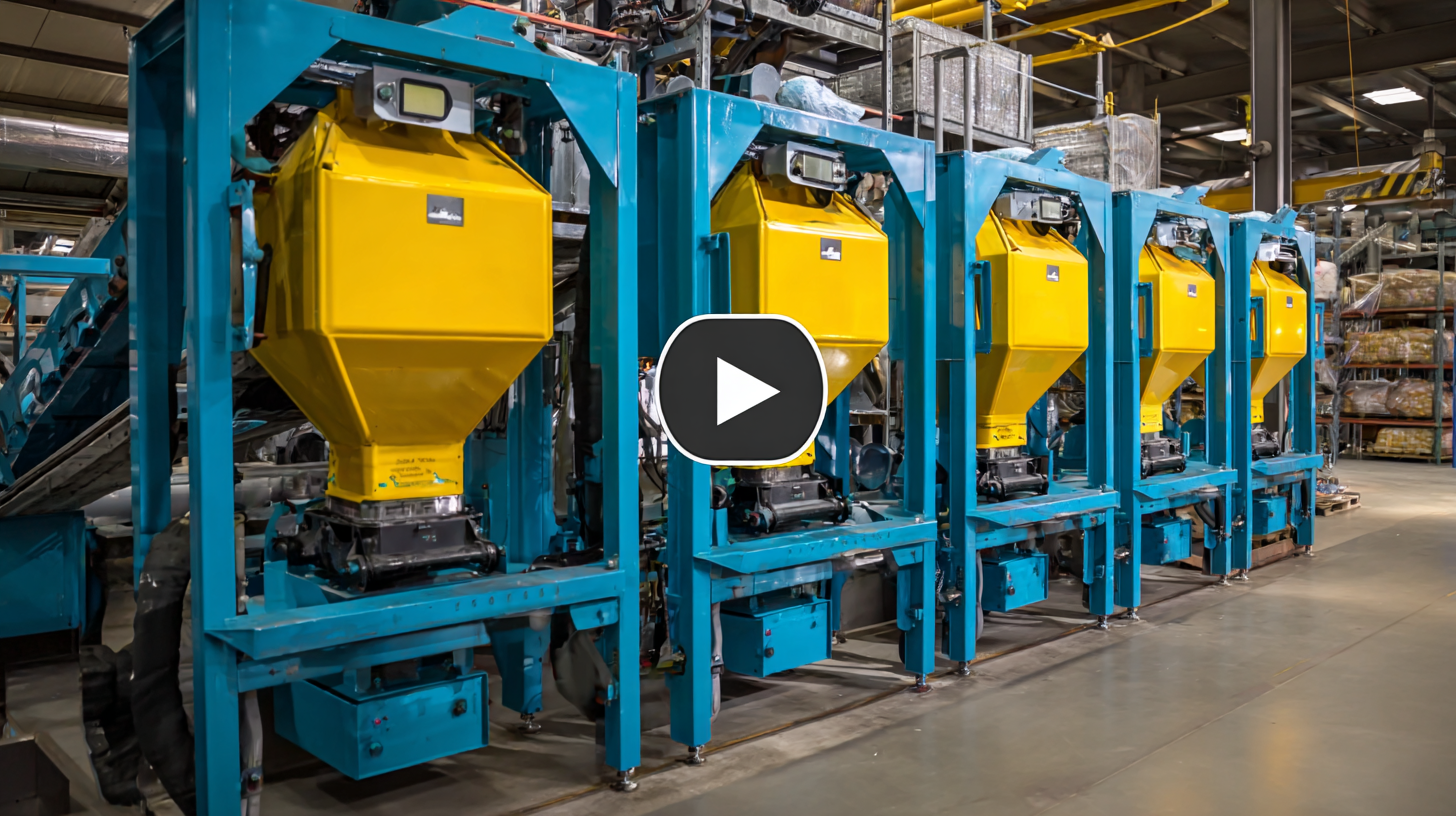
Innovations in Bagging Equipment for Global Market Competitiveness
In today's fast-paced global market, the need for efficient and reliable bagging equipment has never been more critical. Innovations in bagging technology are leading the charge, enabling businesses to enhance productivity while reducing costs. Automated systems, for instance, incorporate advanced sensors and machine learning algorithms, allowing for real-time adjustments during the packaging process. This not only streamlines operations but also minimizes human error, ensuring a consistent and high-quality output that meets diverse industry standards.
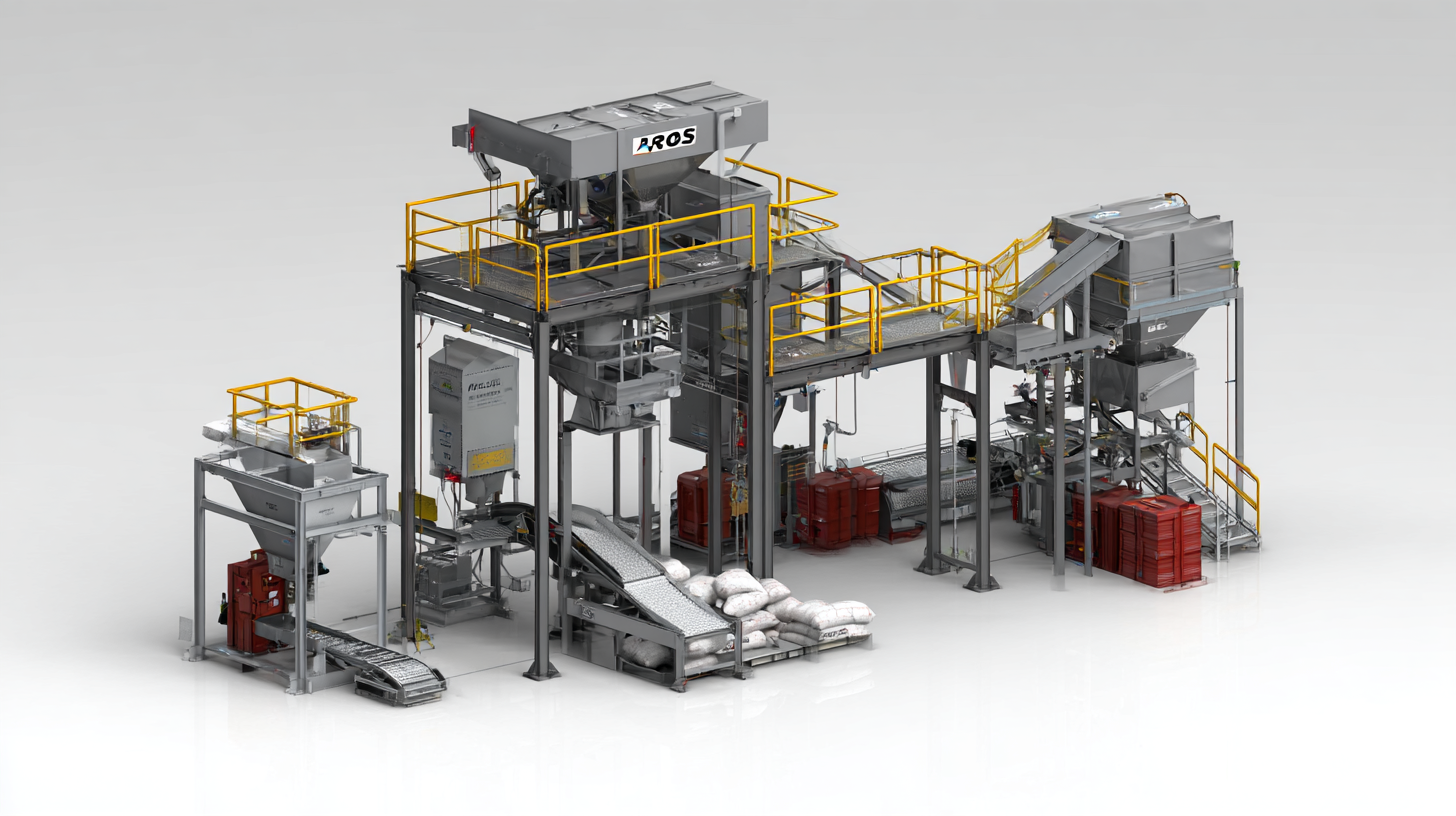
Moreover, eco-friendly materials and designs are gaining traction in bagging equipment innovations. As sustainability becomes a key component of corporate responsibility, manufacturers are developing solutions that utilize biodegradable packaging and energy-efficient machinery. This shift not only appeals to environmentally conscious consumers but also helps companies comply with increasingly stringent regulations. By embracing these innovations, businesses can improve their market competitiveness while contributing to a healthier planet, setting the stage for long-term success in the global marketplace.
Key Factors to Consider for Selecting Reliable Bagging Solutions
When choosing reliable bagging solutions, several key factors should be considered to ensure optimal efficiency and performance. First and foremost, the type of material being bagged plays a crucial role in equipment selection. Different materials—whether powders, granules, or bulk items—require specific bagging systems tailored to their unique properties. Understanding the material's flow characteristics, moisture content, and particle size is essential in selecting an appropriate bagger that prevents issues like jamming or spillage.
Another critical consideration is the desired production rate and scale of operations. High-output facilities may benefit from automated casing and sealing solutions that expedite the process and reduce labor costs. Meanwhile, smaller operations might opt for semi-automatic systems that balance efficiency with investment costs. Additionally, evaluating the bagging equipment’s compatibility with existing production lines, including its adaptability to various bag sizes and materials, is vital for maintaining workflow continuity and minimizing downtime. Emphasizing these factors will lead to a more informed and effective selection process, ultimately enhancing overall productivity and reliability in bagging operations.
The Role of Quality Upgrades in China's Manufacturing Industry
In the competitive landscape of China's manufacturing sector, the emphasis on quality upgrades has become paramount for companies aiming to enhance their operational efficiency and product reliability. According to a report by McKinsey, nearly 70% of Chinese manufacturers are investing in advanced technologies to improve product quality and process efficiency. This trend is particularly noticeable in industries such as electronics and automotive, where precision and reliability are critical.
Quality upgrades not only bolster the reputation of manufacturers but also contribute significantly to their bottom lines. A study from Deloitte indicates that companies that implemented quality improvement processes experienced a 15% increase in overall productivity and a 12% reduction in defects. As businesses in China adopt state-of-the-art bagging equipment tailored to their operational needs, they are better positioned to meet international standards and customer expectations, ultimately tapping into global markets with greater confidence and reliability.
Solutions for Efficient and Reliable Bagging Equipment Selection - The Role of Quality Upgrades in China's Manufacturing Industry
Equipment Type | Quality Upgrade Feature | Efficiency Improvement (%) | Reliability Rating (1-10) | Cost (USD) |
---|---|---|---|---|
Automatic Bagging Machine | High-Speed Control System | 30 | 9 | 15,000 |
Semi-Automatic Bagging Machine | Enhanced Mechanical Parts | 25 | 8 | 10,000 |
Vertical Form Fill Seal Machine | Smart Monitoring System | 20 | 9 | 18,500 |
Bulk Bagging Machine | Automatic Spout Closure | 35 | 10 | 25,000 |
Pallet Bagging Machine | Integrated Palletizer | 28 | 9 | 22,000 |
Comparative Analysis of Bagging Technologies: Efficiency vs. Cost
When selecting bagging equipment, organizations often face the critical decision of balancing efficiency and cost. A comparative analysis of bagging technologies reveals that while high-speed machines promise increased throughput, they can come with elevated upfront costs and maintenance expenses. For instance, automated bagging solutions might streamline the packaging process but require a larger investment in technology and skilled labor to operate. Thus, businesses must carefully evaluate their production needs and budget constraints to determine the most suitable equipment for their operations.
On the other hand, semi-automatic and manual bagging options present a more budget-friendly approach while still achieving satisfactory results in efficiency. These systems might not match the speed of fully automated counterparts but can be advantageous for smaller-scale operations or those producing a diverse range of products. Moreover, the simplicity of operation and lower maintenance requirements often makes them more appealing for companies looking to minimize their operational costs. By weighing these factors, businesses can make informed decisions that align their bagging equipment choices with their overall production goals and financial capabilities.
Comparative Analysis of Bagging Technologies: Efficiency vs. Cost
This chart illustrates the efficiency and cost comparison of various bagging technologies, helping in the selection of suitable equipment based on operational needs.
Case Studies: Success Stories of Efficient Bagging Equipment Implementation
In the pursuit of efficient bagging equipment, real-world businesses are increasingly turning to advanced technologies to enhance their operations. A notable case study highlights a company’s implementation of deep learning algorithms to optimize the bagging process. This strategy resulted in a 30% reduction in waste and significantly improved the speed of production. Moreover, with the inclusion of digital twins technology, businesses can monitor their bagging operations in real-time, enabling predictive maintenance that cuts downtime by an impressive 25%.
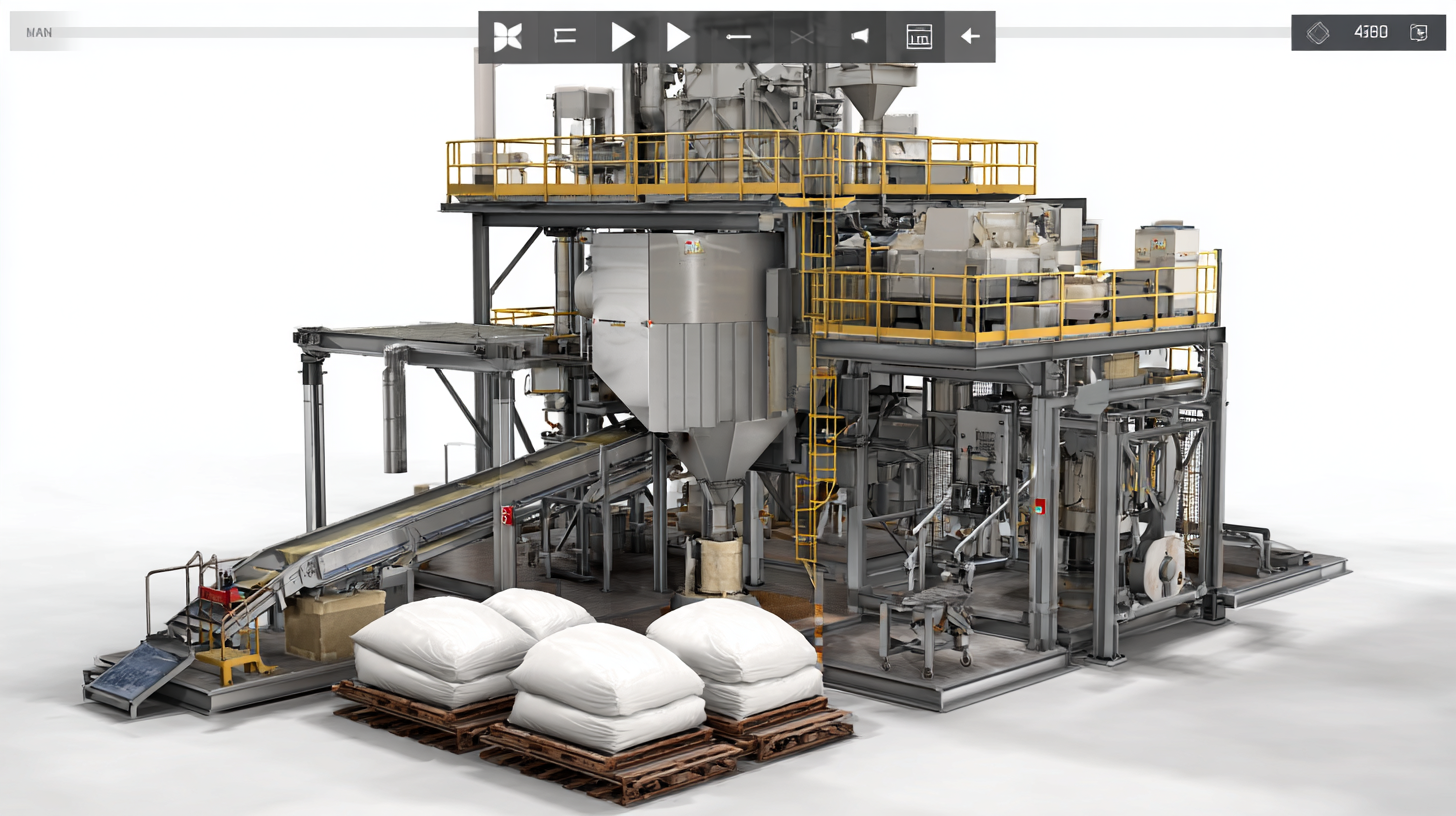
Further success stories depict how the adoption of 5S lean manufacturing principles in a plastic bag manufacturing plant led to a streamlined workflow. By meticulously organizing their workspace, the plant reduced inefficiencies, achieving an overall productivity boost of 15%. These examples illuminate the transformative impact of integrating modern technologies and methodologies in bagging operations, demonstrating that strategic equipment selection not only enhances efficiency but also lays the foundation for sustainable business practices in the industry.